A message from MARANA Water:
In April of 2024, the EPA established Maximum Contaminant Levels (MCL) for six per- and polyfluoroalkyl substances (PFAS). Subsequently, additional Marana Water wells have been affected by the MCL. These new MCLs are much lower than the initial health advisory limits of 70 parts per trillion set in 2016, in which Marana Water had been proactive in the past in delivering PFAS within those respective limits.
Marana Water owns and operates a municipal potable water system located in six individually designated public water systems and has already constructed two (2) existing water treatment campuses (WTCs) which treat water from three potable wells for per- and polyfluoroalkyl substances (PFAS) (particularly perfluorooctyl sulfonate (PFOS) and perfluorooctanoic acid (PFOA)), and 1,4-dioxane.
Prior to the 2024 MCL, in July of 2023, Marana Water commissioned a groundwater treatment feasibility study to evaluate alternatives for groundwater quality improvements. Recent water quality monitoring results for potable production wells not treated at the existing WTCs indicate the presence of PFAS at concentrations exceeding the National Primary Drinking Water Regulations (NPDWR) MCLs for PFAS.
This study analyzed water quality data for all Marana Water potable water production wells and identified areas with concentrations exceeding the MCLs and the existing Health Advisory (HA) level where treatment should be considered. Key information including well production, duty cycles, and most recent water quality data were summarized for each well. Based on this analysis, four water quality improvement sites were developed and include the treatment of both existing and future potable water production wells. Proposed sites are:
- Site 1 – Marana Park (the Town has secured a WIFA loan of $7,179,899 w/$4,500,000 forgivable principal for PFAS Treatment))
- Site 2 – Pioneer Well (the Town has received federal funding of $1.75 million for PFAS Treatment)
- Site 3 – Heritage Park
- Site 4 – Airport NW Well
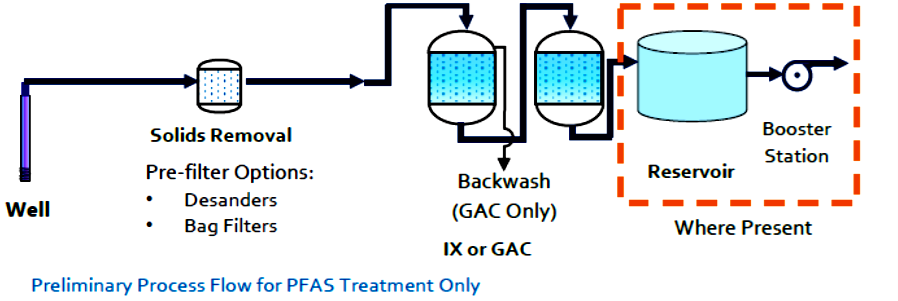
PFAS FAQS:
WHAT IS PFOA AND PFOS? HOW IS IT USED?
PFOA and PFOS are part of a larger group of chemicals called per- and polyfluoroalkyl substances (PFAs) that were widely used in commercial products. They have a strong ability to repel other compounds so they were commonly used as stain protection on fabrics and clothing, non-stick cookware, furniture protection, paper food packaging protection (i.e. microwave popcorn bags, to-go food containers, etc.), as well as in firefighting foams. Most of the companies that use these compounds have phased out their use over the last ten years. However, because the compounds are highly stable and resistant to breakdown, they are commonly still found in the environment.
HOW CAN PFOA AND PFOS IN THE WATER AFFECT MY HEALTH?
The USEPA is continually testing and researching the likelihood that these compounds can be harmful in drinking water. While the research continues, the USEPA has established a lifetime health advisory of 70 parts per trillion for combined concentrations of PFOA and PFOS in order to protect the most sensitive populations: fetuses during pregnancy and breastfed and/or formula-fed infants. Those included in the sensitive populations who consume water from a water system that has shown PFAs levels greater than the health advisory, you may want to take steps to limit or avoid consumption of water directly from the tap. While the department works on the next steps to address this issue, you may be able to treat water at home to reduce the levels of these compounds.
SHOULD I STOP BREASTFEEDING MY INFANT?
EPA encourages women and people who are currently pregnant, nursing, or bottle feeding an infant with formula to consult with their physician regarding concerns related to breastfeeding and potential exposure to chemicals such as PFOA, PFOS, GenX chemicals, and PFBS. For more information about PFAS and breastfeeding, visit the Agency for Toxic Substances and Disease Registry.
WHAT CAN I DO TO REDUCE MY EXPOSURE TO PFAS?
With respect to PFAs, there are two types of treatment that have shown to be somewhat effective in reducing or eliminating these compounds from the water. These treatments are activated carbon and reverse osmosis. Activated carbon filters are relatively common and can be found at most grocery stores and home improvement stores. Examples of these devices are filtering water pitchers and in-line refrigerator filters. Use of these devices has shown a positive effect in reducing or eliminating PFAs, as well as others. Here is a link to a study using University of Arizona research showing the effectiveness of a few of these devices. All in home treatment devices require consistent maintenance and care in order to remain effective.
DOES BATHING/SHOWERING WITH MY TAP WATER PRESENT A HEALTH RISK?
Studies have shown that only a small amount of PFAS can get into your body through skin. Hence, neither bathing nor showering are likely to be primary routes of PFOA, PFOS, GenX chemicals, or PFBS exposure.
CAN I BOIL PFAS OUT OF MY WATER?
No. These chemicals cannot be removed by heating or boiling water.
SHOULD I DRINK BOTTLED WATER?
Deciding whether to buy and drink bottled water is a personal choice. The U.S. Food and Drug Administration (FDA) regulates food, including bottled water. The FDA has not established standards for any PFAS in bottled water at this time, but now that EPA has finalized these standards, FDA is required under Section 410 of the Federal Food, Drug, and Cosmetic Act to evaluate what PFAS standards are appropriate for bottled water.
FDA has analyzed for PFAS in bottled water (carbonated and non-carbonated) through a targeted survey (2016) and through the FDA’s Total Diet Study samples. Results from the studies did not detect PFAS in any sample. The FDA is currently conducting an additional targeted survey for PFAS in bottled water and results will be posted on the FDA’s website when complete. If you have questions about bottled water, please contact the FDA at: 1-888INFO-FDA (1-888-463-6332).
Individuals who are concerned about PFAS in their water may wish to consider in-home water treatment filters that are certified to lower PFAS levels in water. Learn more about these filters: https://www.epa.gov/system/files/documents/2024-04/water-filter-fact-sheet.pdf.
SHOULD I USE A FILTER TO REDUCE LEVELS OF PFAS IN MY WATER?
The more you reduce your exposure to PFAS, the more you reduce your risk. Many water pitcher filters and other home-based water filters are able to reduce the levels of PFAS in drinking water. If you decide to use a filter, look for ones that are certified to reduce PFAS. Be aware that current filters on the market will not yet be certified to reduce PFAS to the new EPA standard, but the added filtration they provide can help reduce your exposure. For more information: https://www.epa.gov/system/files/documents/2024-04/water-filter-fact-sheet.pdf.
IF SYSTEMS HAVE FIVE YEARS TO COMPLY WITH THE RULE, WHAT SHOULD I DO UNTIL THEN IF I'M CONCERNED ABOUT PFAS IN MY WATER?
EPA understands that the PFAS final rule will require some public water systems to make significant investments and that it will take time for them to plan and construct the treatment systems or take other actions they need to comply. That’s why the rule allows systems the flexibility and time to determine the best solutions for their community.
EPA also understands that people may be concerned about the PFAS in their drinking water today. If you are concerned about PFAS in your drinking water, EPA recommends contacting your local water utility. Your utility can tell you more about your drinking water, including what contaminants may be present, if they are monitoring for PFAS, what the levels are, and to see whether any actions are being taken. Some public drinking water systems may not have this information at this time. If you choose to test your water yourself, it is important to use a state-certified laboratory using EPA-developed testing methods. You can also contact your state environmental protection agency or health department and your local water utility to find out what actions they recommend. If you remain concerned about PFAS in your drinking water, you may consider installing in-home water treatment (e.g., filters) that are certified to lower the levels of PFAS in your water. For more information: https://www.epa.gov/system/files/documents/2024-04/water-filter-fact-sheet.pdf.